Creating an inventory system from scratch is a challenging feat. However, it’s also one of the best ways to ensure that you create a system tailored specifically to your uses that keeps track of your inventory. An optimized inventory system can help your business grow to the next level.
In this article, we examine how to create an inventory system for your business and look at what the customized route offers. This is a great way to balance your budget with your needs and find a solution that fits your business perfectly.
Types of inventory management systems
Taking the custom inventory creation route means opening yourself up to a world of options that cater to just about every inventory need you may have. It’s worth looking at the two main categories that these systems fall into to understand their use.
General-purpose systems
General-purpose systems are those intended to perform a wide variety of functions, including but not limited to:
1. Custom inventory management software
Inventory software helps create a solution with unique functionality to cater to the specific needs of a business. This includes functions for inventory control, item management, custom order management, supplier and purchase order management, analytics and reporting, and inventory database management.
2. Inventory database software
The database is the centralized repository for all inventory data collected in an organization. Having a database for inventory management systems allows a business to strike a balance between its performance metrics goals and inventory costs and risks.
The types of inventory databases you can find include:
- Spreadsheets (Google Sheets, Excel, etc.)
- Database apps (LibreOffice Base, Microsoft Access, etc.)
- Custom inventory database software
Some key features we recommend building into a database for inventory management include inventory data storage and navigation, inventory database management, inventory control, and advanced data analytics.
3. Inventory automation system
Inventory automation sees a business create a system where inventory valuation and auditing, inventory levels and location, and inventory ordering and selling are all automated. Large enterprises, for instance, which typically have massive inventories, need ecommerce automation to handle their complex and distributed networks.
Creating an inventory management system plan should include the following elements:
- Inventory planning
- SKU management automation
- Ordering automation
- Costing automation
- Inventory reservation
- Inventory control automation
- Custom order management
- Inventory optimization
- Reverse logistics automation
- Inventory analysis
This will save your business valuable time and ensure that you don’t leave any money on the table due to an inability to keep track of everything necessary.
4. Stock inventory control software
With stock inventory control software, you can monitor the stock costs, levels, and value of items. It’s also a great way to quickly locate items and send alerts when stock replenishment is needed. Custom stock inventory control software aims to introduce the capabilities you need for the job, including:
- Stock database management
- Stock control
- Item management
- Item tracking
- Sales order management
- Purchase order management
- Stock analytics and reporting
A custom stock inventory control system can be integrated with the CRM, ERP, SRM, and inventory management module to facilitate smoother inventory control.
5. Inventory counting software
Inventory counting software helps companies count stock faster and more accurately, enhancing productivity and control. These solutions rely on scanner technology like barcodes and QR codes, the internet of things, and computer vision.
The primary use cases include counting what’s in storage, points of sale, and manufacturing. The way we approach the process can be split into the following implementation plans:
- Barcode or QR code handheld scanners
- RFID-based autonomous devices
- Counting with computer vision
In building inventory counting software, we ensure that the following key features are included:
- Counting automation
- Inventory control
- Replenishment decision-making
- Reconciliation inventory
- Validating inventory placing, pricing, and positioning
- Inventory reporting
This software integrates accounting, hardware, and procurement software to create a nice loop that ensures you can track and adjust stock levels as needed and on time.
6. Inventory optimization
Inventory optimization helps a business avoid overstocking or running out of stock while balancing that need with the cost of holding stock or having a shortage.
In building effective inventory optimization software, we ensure that the following key features are included:
- Demand analysis
- Optimal safety stock computation
- Inventory-related data analysis
- Inventory optimization model management
- Inventory cost analysis
- Prescriptive analytics on inventory replenishment
- Inventory optimization and insights visualization
GET YOUR INVENTORY SYSTEM EXPERTLY DEVELOPED BY OUR TEAM
We’re the one dedicated team you need to automate your inventory management with confidence.
Industry-specific systems
In learning how to create a simple inventory management system for specific industries, it helps to look at some examples of industries and their unique use cases.
- Retail inventory systems: Retailers use these to manage multiple channels and locations, including warehouses, physical stores, online shops, etc. They often have built-in features like point-of-sale integration, barcode scanning, customer loyalty programs, omnichannel sales tracking, and artificial intelligence.
- Manufacturing inventory systems: These are used by manufacturers to plan and control their inventory for producing and distributing goods. Their main features usually include kitting and assembly, quality control, work order management, bill of materials, etc.
- Healthcare inventory systems: These are inventory systems that help healthcare providers and facilities manage their inventory of drugs, equipment, medical supplies, etc. Their main features include expiration date tracking, regulatory compliance management, lot number tracking, and serial number tracking.
As seen from the specific features included in these examples, the inventory design follows the needs and unique functions required by the industry for which it is built.
When do you need custom inventory management software?
In learning how to build an inventory management system, this question is worth asking, as for some businesses, off-the-shelf solutions may be applicable.
Conversely, when you have specific or complex inventory requirements, the custom route may be for you. It allows you to design and build a system that suits your unique inventory operations and goals, including features, integrations, functions, data, etc.
The latter is a more flexible and scalable solution, as you can customize and modify your system as and when your preferences and needs change.
Pros and cons of creating a custom inventory system
Pros
- The inventory can be tailored to your needs and preferences for optimal processes and workflows.
- You get integration with other software and systems you use, including ecommerce, accounting, or point of sale, to create a seamless and efficient data flow.
- You get more flexibility and scalability, allowing you to adjust and expand inventory capabilities as your business grows.
- A custom inventory can be a leg up on the competition, as you can leverage unique features and functions to enhance customer service quality and satisfaction.
Cons
- A custom inventory system can be expensive to build, maintain, and update, as you may need to hire a professional frontend and backend development team to create and support it.
- A custom inventory system could require extensive training and education for your staff, as they may need to familiarize themselves with your system’s unique functions.
- Unless made by expert engineers, custom inventory systems can be prone to technical glitches, crashes, or bugs, as compatibility issues, errors, or failures could affect performance.
Must-have inventory management features
When you plan to build an inventory management system, you must include a base set of features to provide the essential functionalities you need to run a business efficiently.
These functionalities include:
- Barcode scanner: The barcode scanner is a device that reads the black and white lines in a product to tell the system details about the product and its price. The scanner can help speed up inventory processes like receiving, packing, picking, and shipping, eliminating manual data entry and human error.
- Reporting: Reporting allows users to generate and view reports and charts based on inventory data. It’s a way for a business to monitor and evaluate inventory performance, including inventory turnover, value, stock levels, sales trends, etc.
- Forecasting: Forecasting allows the business to predict and plan for future inventory demand and supply.
- Accounting: You need a way to keep track of financial data like prices, gross profit, income statements, and more. The information helps with budget compliance standards like FIFO and LIFO, as well as with average cost methods for determining inventory value.
- Point-of-sale integration: Integration at the point of sale allows businesses to connect their inventory system with their POS to help update inventory data on time whenever sales are made at physical store locations.
- Inventory alerts: The alerts feature allows a business to automate tracking the inventory status and activities. That way, the store knows when stock is low or high, when products expire, what orders are pending, what shipments are overdue, and more.
- Automatic reordering: Automatic reordering ensures that stock is replenished on time, without human intervention, to maintain optimal stock levels at all times.
- Logistics: The logistics feature allows users to manage their inventory distribution and delivery. It can help users optimize their inventory flow across channels and locations.
8 steps to develop your custom inventory management software
Finally, we get into how to make inventory management software. What are the best practices? Drawing from our experience, we have boiled it down to the following steps.
1. Create a requirements list
To start, your first step should be defining the scope and objectives of your inventory management software, including the features, functions, data, users, and so on. You have to collect and analyze the needs of stakeholders, including your suppliers, managers, and employees.
2. Develop an architecture and design of the system
Inventory management system design calls for creating modules, components, interactions, interfaces, etc. You can start with a high-level and low-level design of your system that meets the requirements gathered.
You can use various methods and tools to develop the architecture and design of the system, including flowcharts, UML diagrams, wireframes, and so on.
3. Create a tech stack
Creating a tech stack means selecting the technologies and tools that you will use to build and run the inventory management software, including:
The tech stack is determined by your system’s needs and goals, budget, and timeline. It’s also worth considering the compatibility and integration of your tech stack with other systems or services that you can use or connect with.
4. Set up the development and testing process
This is where you put your technology stack into action and test how well it works.
With EPAM Startups & SMBs, you can get access to the experts who do this. We use various tools and techniques to support the development and testing stages, including code editors, frameworks testing, IDEs, version control systems, and more.
Contact us today to get help with any aspect of the development and testing process. We’ll help you with the entire process, including coding, debugging, documentation, analysis, and everything in between.
5. Fix and tune
After testing the software, the next step is to fix any errors you find before rolling out the system for wide usage.
You can leverage various tools and techniques for fixes and fine-tuning, including:
- Code analysis
- Profiling tools
- Debugging tools
- Profiling and benchmarking techniques
- Refactoring and reengineering
- Algorithm and patterns optimization
- Parallelization and distribution
The optimization process not only ensures that the software will work correctly once in use but also that it performs efficiently.
6. Set up integrations with other systems
You can then integrate your inventory management software with other systems or services related or relevant to your business operations, including sales, accounting, logistics, purchasing, and so on. Ensure that inventory data is synchronized and consistent across all services or systems.
7. Start user training
To make the most of your inventory software, it’s worth including the necessary time and resources to train your users on what they can do with it. The training material and sessions must be clear and comprehensive regarding accessing and navigating the inventory system, performing various functions, troubleshooting known issues, and more. You can deliver this via manuals, videos, workshops, and webinars.
8. Create a support service
Finally, you must provide ongoing support and maintenance for your inventory management system. That will ensure that it runs smoothly and that any issues are quickly resolved to avoid bottlenecks and potentially costly delays.
Our best practices in inventory management development
For more insights on how to make an inventory system, we have two case studies that showcase best practices in optimizing inventory management.
Case 1: A digital marketing platform with DevOps automation for Bacardi
From the decisions taken during this project, best practices for inventory management development emerge, including:
- The ability to manage the inventory of digital assets more efficiently, with the ability to view, update, and deploy them in an automated and centralized way.
- Optimizing the inventory performance and availability by reducing downtime, bottlenecks, and errors in the deployment process.
- Aligning the inventory strategy with business goals and customer needs, powered by the ability to deliver consistent, innovative, and engaging digital experiences across brands.
Case 2: Combining Sitecore CommerceConnect and SAP Customer Experience
In this second case, the project’s objectives align with the best practices of inventory management development in the following ways:
- Combining Sitecore CommerceConnect and SAP Customer Experience creates a powerful and integrated solution, leveraging the strengths of both platforms.
- Syncing products between SAP Customer Experience and Sitecore 10x faster reduced the time and effort required to manage the inventory data.
- Saving thousands of project hours compared to starting from scratch focused the project teams on improving customer experience and adding to revenue.
- Providing ready-to-use features, including checkout, catalog, order management, shopping cart, real-time price and inventory, and user profiles, covers some essential aspects of inventory management development.
LEVERAGE OUR PROVEN EXPERIENCE FOR YOUR INVENTORY MANAGEMENT NEEDS
Contact us for custom inventory system development. At EPAM Startups & SMBs, we build custom projects suited to our clients’ needs.
Conclusion
In covering how to make inventory management software, our journey has taken us through the components, features, and best practices for developing an efficient solution. It’s a process that any business can undertake, and one that may have numerous benefits to those whose businesses most need one.
FAQ
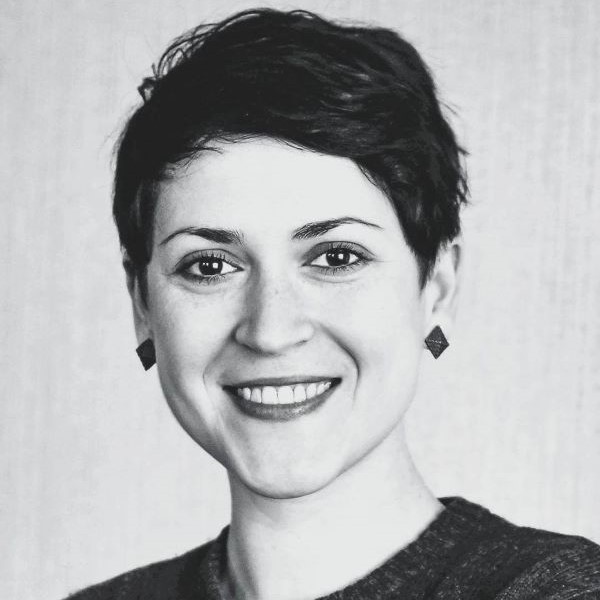
Expert digital communicator and editor providing insights and research-based guides for technology buyers globally.
Expert digital communicator and editor providing insights and research-based guides for technology buyers globally.
Explore our Editorial Policy to learn more about our standards for content creation.
read more